MATLAB EXPO 2019
See Full Details for Each MATLAB EXPO Location Below
Overview
MATLAB EXPO brought together engineers, researchers, and scientists to hear real-world examples, get hands-on demonstrations, and learn more about the latest features and capabilities of MATLAB and Simulink.
Featured Sessions
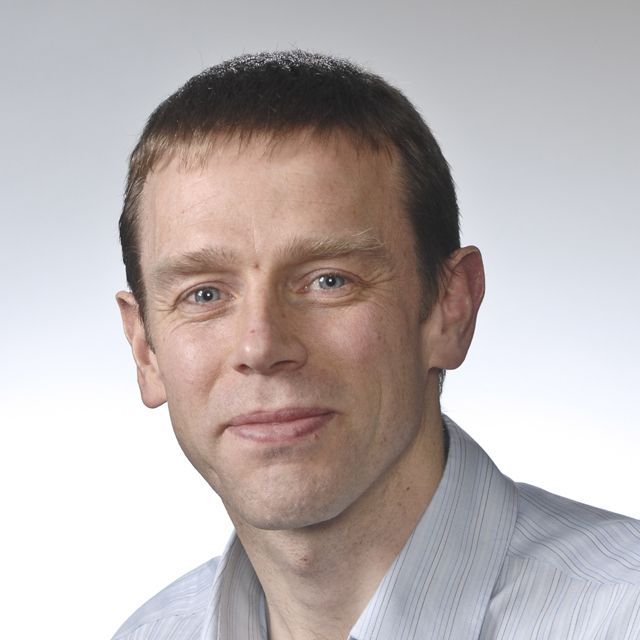
Beyond the ‘I’ in AI
Chris Hayhurst, MathWorks
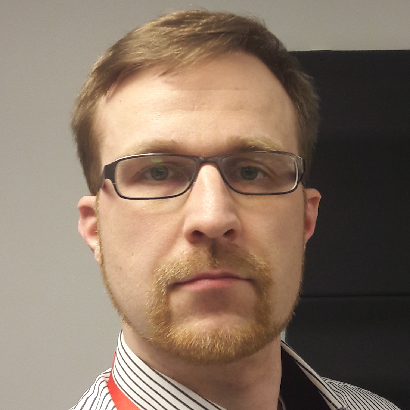
Experiences of using Model-Based Design in Development of Control Software for Electric Drives
Tapani Hyvämäki, Danfoss
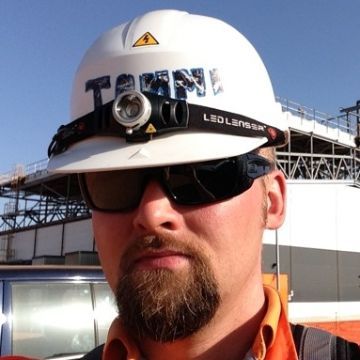
Model-Based Design in Industrial Automation
Tommi Latva, Wärtsilä
Agenda
Tracks
A
B
Registration
Welcome and Introduction
MathWorks Keynote: Beyond the ‘I‘ in AI
User presentation from Wärtsilä: Model-Based Design in Industrial Automation
Break
What’s New in MATLAB and Simulink
User presentation from Danfoss: Experiences of using Model-Based Design in Development of Control Software for Electric Drives
Lunch and Exhibition
Deep Learning and Reinforcement Learning Workflows in AI
Developing Digital Control for Power Converters
Break and Exhibition
Becoming a Data-Centric Engineering Team: Catching up to the Data Deluge
Master Class: Adopting Model-Based Design for FPGA, ASIC, and SoC Development
Deploying AI/ML for Near Real-Time Manufacturing Decisions
Simplifying Requirements Based Verification with Model-Based Design
Master Class: Predictive Maintenance with MATLAB
Power Electronics HIL with Simscape to HDL Conversion
End of sessions
Demo Station Information
Attendees visited the demo stations to discuss their challenges and ideas with MATLAB and Simulink experts, and saw demos showcasing the latest features in MATLAB and Simulink, including:
- Machine Learning & Deep Learning
- Predictive Maintenance
- Integrating MATLAB into Enterprise Systems, Clusters, or Clouds
- Power Electronics Control Design
- Verification & Validation in Model-Based Design
- Implementing MATLAB and Simulink Design on FPGA, ASIC & SoC Devices
Overview
MATLAB EXPO brought together engineers, researchers, and scientists to hear real-world examples, get hands-on demonstrations, and learn more about the latest features and capabilities of MATLAB and Simulink.
Featured Sessions
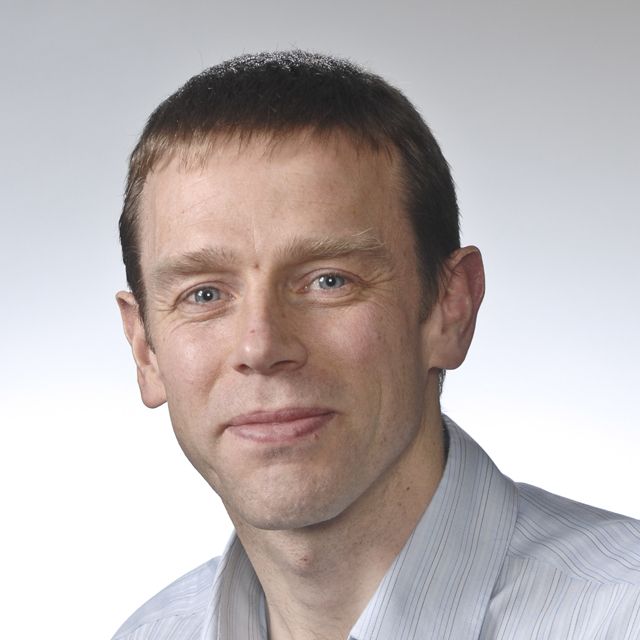
Beyond the ‘I’ in AI
Chris Hayhurst, MathWorks
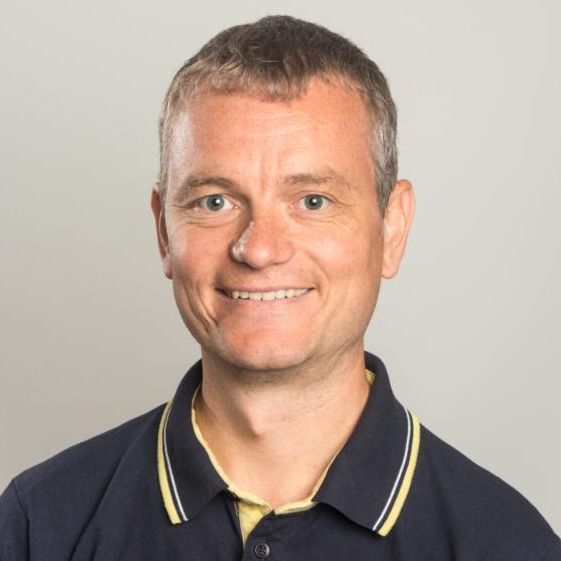
Deep Learning for Sonar Applications
Karl Thomas Hjelmervik, FFI
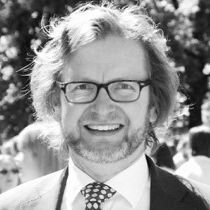
Model Based Design using MathWorks Toolchain at Getinge in Solna
Magnus Nord, Getinge Group, Maquet
Agenda
Tracks
A
B
Registration
Welcome and Introduction
MathWorks Keynote: Beyond the ‘I‘ in AI
User presentation from FFI: Deep Learning for Sonar Applications
Break
What’s New in MATLAB and Simulink
User presentation from Getinge: Model-Based Design using MathWorks toolchain at Getinge in Solna
Lunch and Exhibition
Deep Learning and Reinforcement Learning Workflows in AI
Becoming a Data-Centric Engineering Team: Catching up to the Data Deluge
Master Class: Adopting Model-Based Design for FPGA, ASIC, and SoC Development
Deploying AI/ML for Near Real-Time Manufacturing Decisions
Break and Exhibition
Developing Digital Control for Power Converters
Simplifying Requirements Based Verification with Model-Based Design
Master Class: Predictive Maintenance with MATLAB
Power Electronics HIL with Simscape to HDL Conversion
End of sessions
Demo Station Information
Attendees visited the demo stations to discuss their challenges and ideas with MATLAB and Simulink experts, and saw demos showcasing the latest features in MATLAB and Simulink, including:
- Machine Learning & Deep Learning
- Predictive Maintenance
- Integrating MATLAB into Enterprise Systems, Clusters, or Clouds
- Power Electronics Control Design
- Verification & Validation in Model-Based Design
- Implementing MATLAB and Simulink Design on FPGA, ASIC & SoC Devices
Overview
MATLAB EXPO brought together engineers, researchers, and scientists to hear real-world examples, get hands-on demonstrations, and learn more about the latest features and capabilities of MATLAB and Simulink.
Featured Sessions
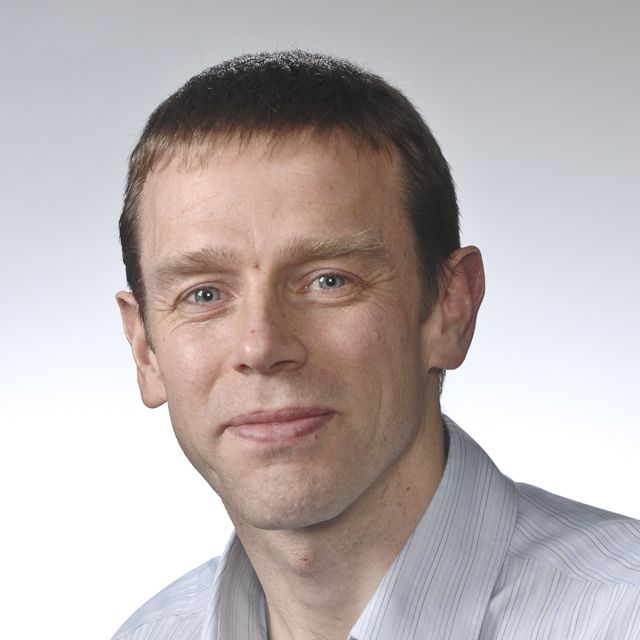
Beyond the ‘I’ in AI
Chris Hayhurst, MathWorks
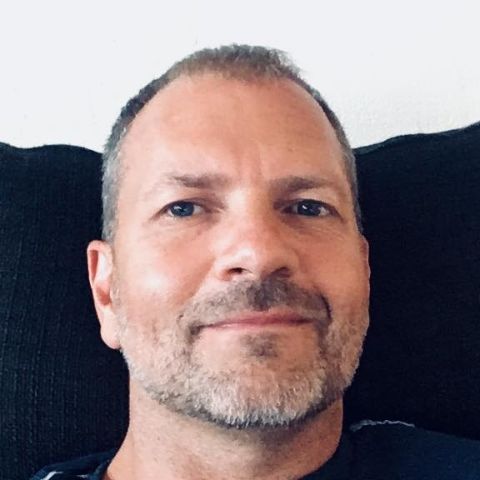
A Journey with Model-Based Design
Per Hagen Nielsen, Vestas Wind Systems A/S

System Simulation of Linear Actuator System
Peter Gravesen, LINAK A/S
Agenda
Tracks
A
B
Registration
Welcome and Introduction
MathWorks Keynote: Beyond the ‘I‘ in AI
User presentation from Vestas Wind Systems: A Journey with Model-Based Design
Break
What’s New in MATLAB and Simulink
User presentation from LINAK: System Simulation of Linear Actuator System
Lunch and Exhibition
Deep Learning and Reinforcement Learning Workflows in AI
Becoming a Data-Centric Engineering Team: Catching up to the Data Deluge
Master Class: Adopting Model-Based Design for FPGA, ASIC, and SoC Development
Deploying AI/ML for Near Real-Time Manufacturing Decisions
Break and Exhibition
Developing Digital Control for Power Converters
Simplifying Requirements Based Verification with Model-Based Design
Master Class: Predictive Maintenance with MATLAB
Power Electronics HIL with Simscape to HDL Conversion
End of sessions
Demo Station Information
Attendees visited the demo stations to discuss their challenges and ideas with MATLAB and Simulink experts, and saw demos showcasing the latest features in MATLAB and Simulink, including:
- Machine Learning & Deep Learning
- Predictive Maintenance
- Integrating MATLAB into Enterprise Systems, Clusters, or Clouds
- Power Electronics Control Design
- Verification & Validation in Model-Based Design
- Implementing MATLAB and Simulink Design on FPGA, ASIC & SoC Devices
Are you Ready for AI? Is AI Ready for You?
9:30 - 10:30
Lorem ipsum dolor sit amet, consectetur adipiscing elit, sed do eiusmod tempor incididunt ut labore et dolore magna aliqua. Ut enim ad minim veniam, quis nostrud exercitation ullamco laboris nisi ut aliquip ex ea commodo consequat. Duis aute irure dolor in reprehenderit in voluptate velit esse cillum dolore eu fugiat nulla pariatur. Excepteur sint occaecat cupidatat non proident, sunt in culpa qui officia deserunt mollit anim id est laborum.
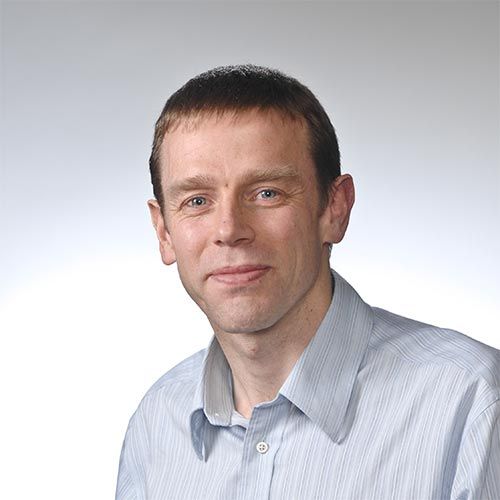
Chris Hayhurst
MathWorks
Chris Hayhurst leads the MathWorks Consulting Services organization in Europe, managing a group of highly experienced engineers covering many industries and every aspect of MATLAB and Simulink product capability. At MathWorks, Chris has worked in many industries including automotive, aerospace, construction and agricultural equipment, electrical machines, and industrial equipment. Prior to joining MathWorks in 1997, Chris was involved in the design of flight control systems for helicopters, working with Simulink to model future helicopter dynamics and control strategies. He holds a degree in electrical engineering from Cambridge University. He is also active in the Institute of Engineering and Technology and in encouraging engineering and computing education in schools.
Beyond the ‘I’ in AI
Insight. Implementation. Integration.
AI, or artificial intelligence, is transforming the products we build and the way we do business. It also presents new challenges for those who need to build AI into their systems. Creating an “AI-driven” system requires more than developing intelligent algorithms. It also requires:
- Insights from domain experts to generate the tests, models, and scenarios required to build confidence in the overall system
- Implementation details including data preparation, compute-platform selection, modeling and simulation, and automatic code generation
- Integration into the final engineered system
Join us as Chris Hayhurst demonstrates how engineers and scientists are using MATLAB® and Simulink® to successfully design and incorporate AI into the next generation of smart, connected systems.
Presenter: Chris Hayhurst
Chris Hayhurst leads the MathWorks Consulting Services organization in Europe, managing a group of highly experienced engineers covering many industries and every aspect of MATLAB and Simulink product capability. At MathWorks, Chris has worked in many industries including automotive, aerospace, construction and agricultural equipment, electrical machines, and industrial equipment. Prior to joining MathWorks in 1997, Chris was involved in the design of flight control systems for helicopters, working with Simulink to model future helicopter dynamics and control strategies. He holds a degree in electrical engineering from Cambridge University. He is also active in the Institute of Engineering and Technology and in encouraging engineering and computing education in schools.
System Simulation of Linear Actuator System
LINAK Linear electrical actuators are mechatronic systems developed for a wide range of applications including medical beds, couches and patient lifters, beds for home, furniture and a wide range of industrial applications for agriculture machinery.
Simulink/Simscape tools have been successfully used to simulate the entire actuator system including AC/DC power supply, motor controller, motor, gear, spindle/nut rotation to linear transmission and including both electrical, mechanical and thermal interaction between all sub-systems.
This presentation will focus on the methods and “tricks” used to make a complete model without considering all geometrical details of or individual components, but rather focus of functional elements built with Simulink/Simscape library elements.
This includes:
- A Power supply and Motor controller with power and current limitations as well as sensor inputs
- Drive line components with thermal ports and thermal system interaction
- Solving the thermal modeling challenge related to moving parts by changing thermal coupling as a function of actuator position
- Use of parameters, which are automatically calculated by an Excel-template file for subsequent easy import into MATLAB environment
Presenter: Peter Gravesen
M.Sc Electrical Engineering, Industrial PhD in Microsystems and post doc. at MIT.
Developed a capacitive MEMS accelerometer during PhD study and continued work with MEMS pressure sensors, micro-fluid systems, EAP actuators and other sensors and actuator technologies with Danfoss A/S.
Co-founder of CeQur venture company with focus on Insulin pump R&D, manufacturing processes for microfluidic components, mechanical and fluid simulation of complex miniature molded pump system and clinical testing.
Now at LINAK A/S with responsibility for new technology projects including sensor technologies, Sound & Vibration Analysis, digitalization as well as extended use of various advanced simulation tools.
Author or co-author of more than 30 publications and 26 patents and patent applications.
A Journey with Model-Based Design
A practical path for a full Model-Based Design approach at Plant Control Engineering at Vestas over 5 years. In 2014 the department started an investigation to change the way the department work to a Model-Based Design approach. The presentation will cover what challenges the department had before that approach. Pre-study. Reasons for decision. Ambitions. Unforeseen challenges. Education. New roles. MathWorks involvement. Where are we now and what is next.
Presenter: Per Hagen Nielsen
Per Hagen Nielsen is a Control System Software Architect at Vestas Wind Systems who works as designer for various aspects of wind power plant control. He is an educated Electronic Engineer and has 20 years of experience developing control systems and embedded software systems.
Model-Based Design in Industrial Automation
It’s well known that industrial automation is lagging 20 years behind of all progress – securing the production is more important than riding on the wave of the latest technology innovations. This is due to the fact that market starts to demand more integration to digitalised world and more sophisticated development environments.
Wärtsilä has made a step towards autonomous power plants where human interactions are coming more and more insignificant. With this conscious choice Model-Based Design is playing significant role by providing methods to build a system which is tested at the earliest stage. This prevents design errors and ensures flawless operations from day one.
One key-factor for Wärtsilä’s success has always been standardisation and modularisation of plants and this has not and will not change even in the future. Therefore it’s important to create a development environment which supports this way of working. MATLAB® and Simulink® are the best available overall toolset for this job.
Presenter: Tommi Latva
41 year old Automation engineer with more than 20 years of experience in field of automation. He has worked in automation projects in five continents at all stages from design, installation, commissioning and service.
Experiences of using Model-Based Design in development of control software for electric drives
Danfoss has been using Model-Based Design in the development of motor and grid converter control software for more than 15 years. MathWorks products have had a central role in this development. Since the beginning, simulation of power electronics systems has been one of the back-bones of the development, but during the years, new features of MATLAB and Simulink software have been adopted and taken into use. These include production code generation, HIL setup code generation, unit testing, system testing and version control just a few to mention. Also by executing the code generation and tests automatically and by utilizing parallel computing has significantly speeded-up the development and improved quality. The use of MathWorks products in a product development organization of more than fifty MATLAB/Simulink users has lead to development of a set of common modeling practices and rules that are crucial to maintain a fluent and agile development process.
Presenter: Tapani Hyvämäki
Tapani Hyvämäki works as a Control Engineer at Danfoss in Tampere Finland. His educational background is in Engineering Physics and Mathematics. He has worked in industry for 8 years, mainly in the field of control engineering, and has been active user of MathWorks products for roughly 15 years. He is specifically interested in computationally efficient control algorithm implementations, motor and grid converter control as well as development of model-based design methods and tools. He has contributed to taking Model-Based Design into use as the main control software development approach at Danfoss.
Model-Based Design using MathWorks toolchain at Getinge
At the Getinge Group facility in Solna we invent, develop and manufacture high-end ventilators and anesthesia machines. The world’s first servo-controlled ventilator was designed at this very site in 1971, making the start of an era of highly sophisticated medical equipment developed in Solna. Our products now include state of the art functions such as NAVA (Neurally Adjusted Ventilator Assist) and AGC (Automatic Gas Control). We are world leader in high-end ventilation.
The presentation covers all areas were the MathWorks toolchain is used, including system identification, physical modeling, external mode, control design, logic design using Stateflow, unit tests, PIL and production code delivery
The topics listed above will be flavored with lessons learned from thesis projects, product development and research projects. During the speech I’m also going to answer some questions. How is MathWorks toolchain helping in achieving a Model-Based Design process at Getinge in Solna? In what areas does is the help sufficient and where do we hope for improvements?
Presenter: Magnus Nord
Control Systems Engineer with a M.Sc. from Linköping, Sweden. Thesis study on the mathematical comparison between a single layer neural network and a double layer neural network when used for system identification. Control system engineer experience from fighter aircraft, telecom and medical equipment. System engineer experience and 10+ years project management experience in medical equipment domain. Research expat experience in the USA and in Germany. Last 10 years focusing on Model-Based Design, adding more and more Simulink functionality into our products. Special interests are system identification, AI, rapid prototyping and SoC design with Simulink at its core.
Deep Learning for Sonar Applications
Operation of high-resolution, broadband anti-submarine warfare (ASW) sonars in littoral waters is challenging, since the presence of sea mounts, underwater ridges and other topographic features causes increased false alarm rates.
Conventionally, high false alarm rates have been handled by increasing the threshold applied in the sonar detection algorithm or by employing classification algorithms for instance through the use of feature extraction and machine learning algorithms. In recent years, for related applications, deep neural networks applied directly on raw data have been shown to outperform conventional machine learning algorithms that are fed with features.
Here we employ a deep learning algorithm on a sonar data set. The sonar data set is processed using conventional algorithms. The resulting detections are classified by hand as either false alarms or target detections. The target is here a one meter diameter pipeline. The detections are split into training, validation and test sets. Matched filter data from a window surrounding the resulting detections are extracted and used to train a deep neural network.
Presenter: Karl-Thomas Hjelmervik
Karl Thomas Hjelmervik is a scientist at the Norwegian Defence Research Department (FFI). His main academic interests include sonar processing, acoustic modelling, and classification. He received his B.S. and M.S. degrees in physics at the University of Bergen in 1999 and 2002, and later finished his PhD in acoustics and signal processing at the Norwegian University of Science and Technology in 2011.